There are many factors influencing the chemical resistance of
plastic emulsion pumps, involving material selection, design characteristics, and operational environment. Here are some key factors:
Material Selection:
The choice of materials for
plastic emulsion pumps is crucial. Different types of plastics exhibit varying chemical resistances. Common plastic materials include polypropylene, polyethylene, polyvinyl chloride, polytetrafluoroethylene, etc. The selection of suitable materials depends on the chemical composition of the handled liquid, including acidity, alkalinity, solvents, oils, and other chemicals.
Chemical Properties of Substances:
Different chemicals possess different corrosive and erosive properties. Certain chemicals may have a more pronounced impact on specific types of plastics, so consideration of the chemical composition of the handled liquid is essential when selecting a pump.
Temperature:
Temperature significantly affects the performance and chemical resistance of plastics. Some plastics may become more brittle at high temperatures, making them prone to deformation or loss of elasticity. Therefore, when using plastic emulsion pumps in high or low-temperature environments, it's crucial to ensure the selected material maintains stability under these conditions.
Fluid Properties:
The nature of the emulsion also affects the chemical resistance of the pump. Emulsions may contain emulsifiers, surfactants, or other chemical additives that can have varying effects on pump materials.
Design Characteristics:
The design features of the pump, such as sealing structures, valve types, and connection methods, also influence its chemical resistance. Sealing performance and component connection methods can affect the permeation of chemicals into the pump, thereby impacting its stability.
pH Value:
The acidity or alkalinity of the liquid also has an impact on the chemical resistance of plastic emulsion pumps. Some plastics are more sensitive to acidic or alkaline environments, so consideration of the pH value of the handled liquid is necessary when choosing materials.
Surface Coatings:
Some
plastic emulsion pumps may have special surface coatings to enhance their chemical resistance. These coatings can increase the hardness, corrosion resistance, and wear resistance of the plastic surface.
Operating Conditions:
Operational conditions, including the pump's operating pressure and flow rate, are also factors influencing chemical resistance. Under high-pressure or high-flow conditions, plastic emulsion pumps may face more challenging chemical environments.
Chemical Concentration:
The concentration of chemicals directly affects the degree of corrosion on plastics. For some chemicals, low concentrations may be acceptable, but at high concentrations, it could lead to severe material corrosion.
Considering these factors comprehensively is key to ensuring that plastic emulsion pumps exhibit good resistance in chemical environments. Careful consideration of material selection, pump design, and operational conditions is necessary to meet the specific requirements of the application.
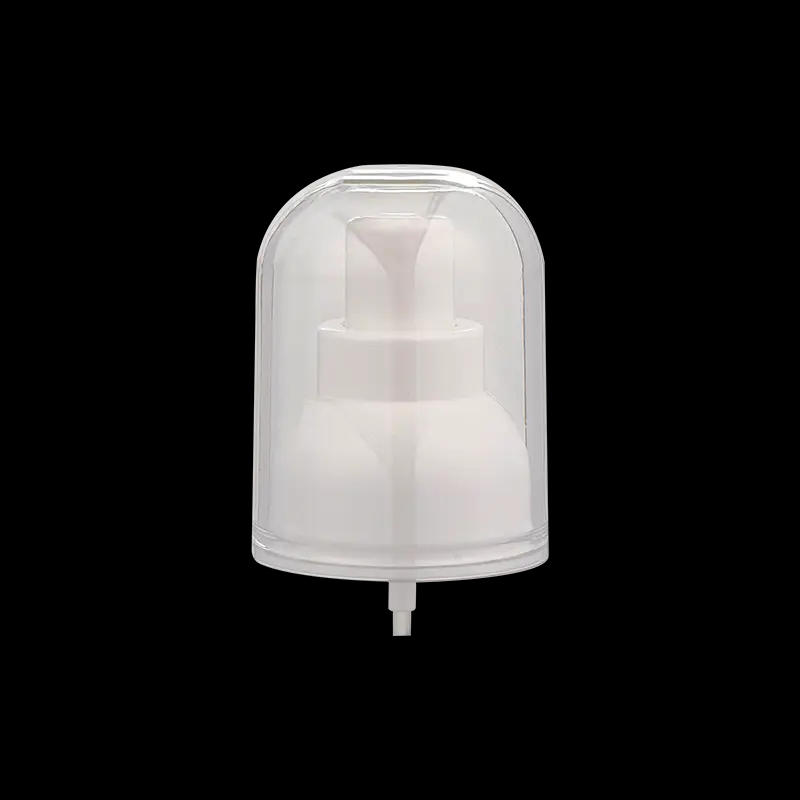